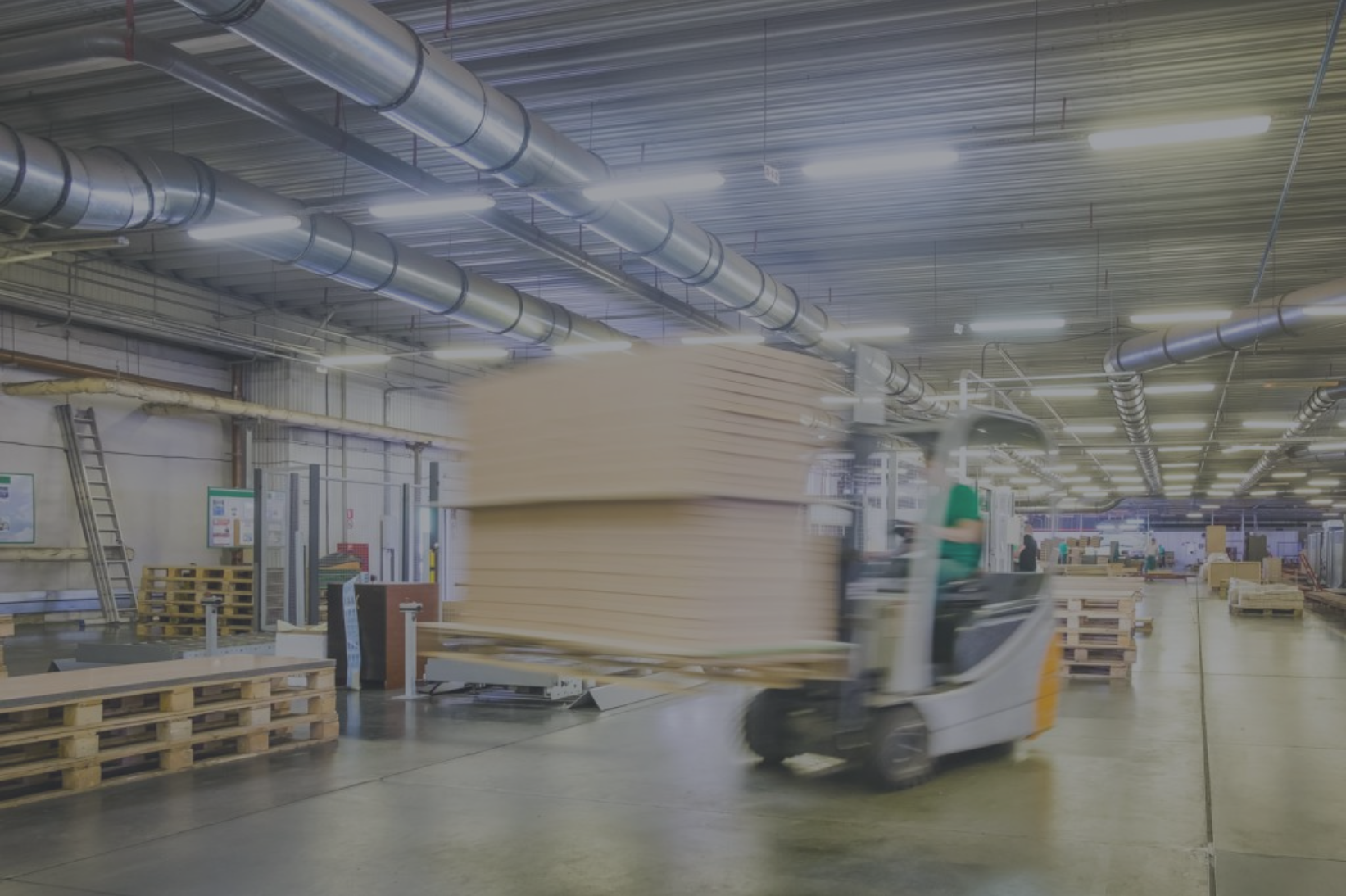
Gallus
Fixed Barcode Scanning System in the Packaging Plant of Magyar Cukor Zrt.
In the autumn of 2016, the IT manager of Magyar Cukor Zrt. contacted our company to find a solution to check the barcodes on the packed goods at the end of the assembly line in the packaging plant and to identify products.
Packed products on pallets and products arriving in big bags containing 1000kg of bulk sugar must be identified in the packaging plant. In the past, it was difficult to track the progress of production and movement of finished goods within the warehouse. The barcodes placed on the products by an automatic labelling machine were checked by employees and the barcode verification was performed manually. Data may not have been recorded in the ERP system after manual scanning, so inventory figures were not accurate.
The task, therefore, is to automatically check the presence of labels and the readability of the barcodes and to develop a system that allows forklift trucks to decide to move only correctly labeled products to the finished goods warehouse. This means that only products with readable labels can be sent to the warehouse, as this guarantees that product information is automatically recorded in the ERP system.
The hardware base of our automated barcode verification solution is provided by a Raspberry Pi board, to which additional signal and voltage converters are connected to manage the various devices operating at different voltages.
At the end of the assembly line at the packaging plant, photocell sensors are located at 4 points that can determine if there is a product at that specific point. When a package passes through the first point, the photocell sensor sends a pulse to the Raspberry, which in turn transmits the command to the camera system to begin scanning. Labels are scanned by the smart camera system provided by Cognex.
After scanning, the camera system stores the product identification code in a file (in a predefined location and format). From this file, Raspberry reads the code, then compares the code with a list in an MS SQL database and checks if the scanned code exists in the database. If so, it assigns a corresponding state to the product (green state).
If not, or if it finds an error code in the file, it assigns an error state to the product (red status). With the help of color-coding, the forklift operator knows whether the product has been successfully identified and can be transported to the finished goods warehouse. If for some reason the barcode was not read successfully, it can still be scanned with a handheld reader at the end of the assembly line.
As the product is removed from the roller conveyor by the forklift operator, each pallet / big bag moves forward towards the end of the roller conveyor. As all products move forward, the display screen is constantly updated to reflect the signals sent by the sensors.
With the new automatic scanning system, Magyar Cukor Zrt. receives continuously updated and accurate inventory data and meets quality requirements more easily. Products move faster from the production line to the warehouse because forklift operators can easily determine that the product has been identified and the goods can be transported. The new system also reduces labor costs.